Erik Larnøy
Seniorforsker
Sammendrag
Det er ikke registrert sammendrag
Sammendrag
Det er ikke registrert sammendrag
Sammendrag
The study investigated the production process and properties of a new wood-based material called Bioblocks. This sustainable composite is made from medium-density-fibreboard (MDF) residues, citric acid and either sorbitol or hexanediol. The process involves mixing in-water diluted chemicals with the MDF residues and curing the mixture in a laboratory oven to esterify the sorbitol and wood components with citric acid. A design of experiment was used to determine the influence and optima of the different process factors, and an optimised trial further investigated the material properties. The density distribution, compression strength, and TS after 24 h immersion in water according to EN 317 of the Bioblocks were tested. The first trial showed that mainly the amount of water added impacts the product’s properties. The optimised material achieved a sufficient density distribution with an average density of about 420 kg/m3, a compression strength of up to 3.5 N/mm2, and a TS of about 2%. Therefore, Bioblocks are a promising natural material to use waste MDF and substitute fossil, unsustainable materials.
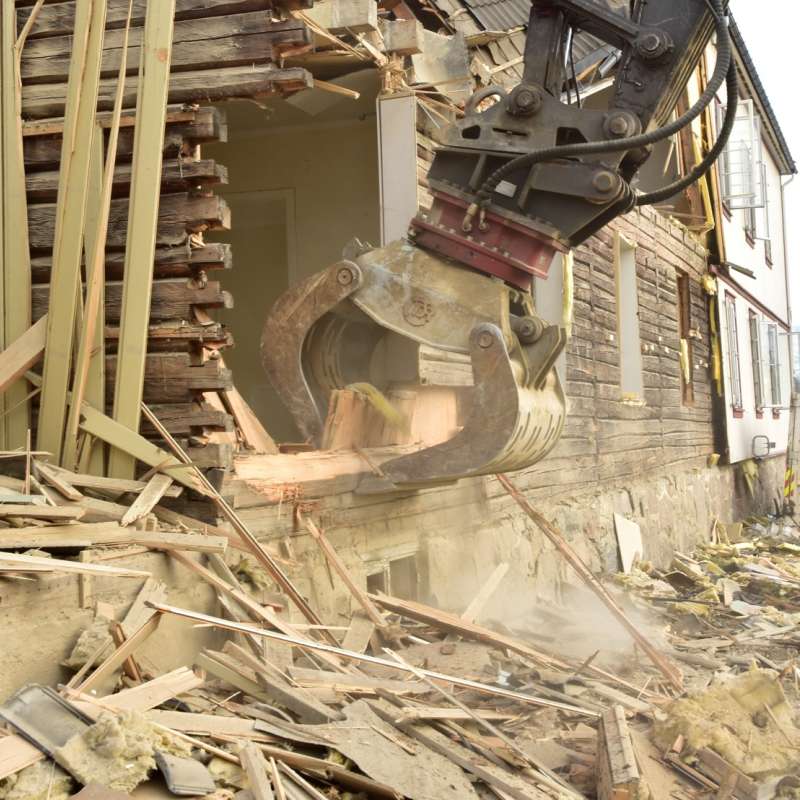
Divisjon for skog og utmark
Sirkulær bruk av tre for økt bærekraft og innovasjon (CircWOOD)
CircWOOD skal undersøke aspekter ved trebruk i den norske økonomien, med særlig vekt på ombruk av returtre i byggeprosjekter, og returtre som råstoff i dagens treindustri.
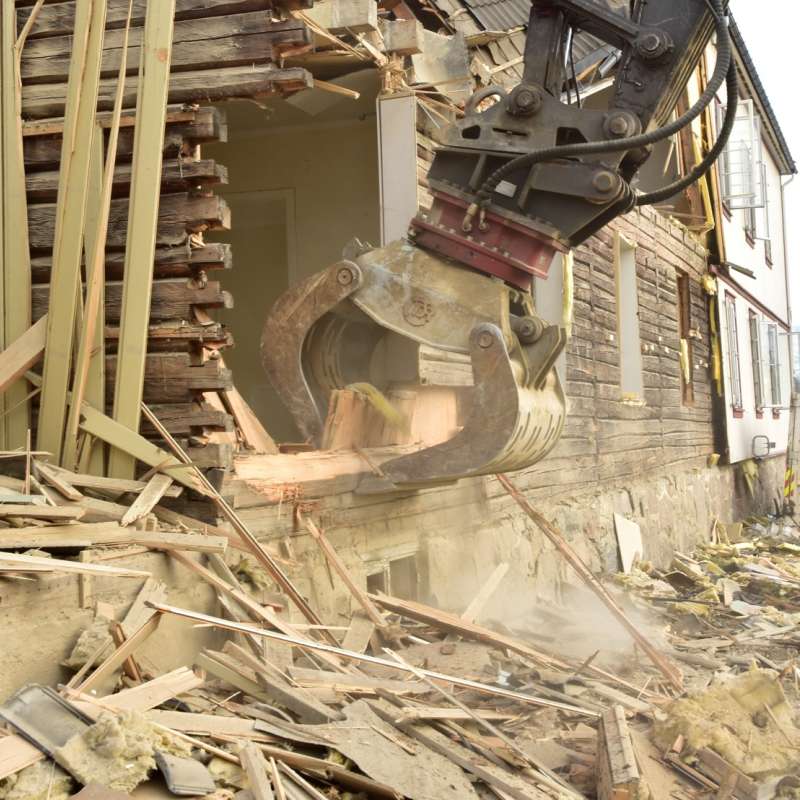
Divisjon for skog og utmark
Circular use of wood for increased sustainability and innovation (circWOOD)
circWOOD will investigate aspects of wood use in the Norwegian economy, with particular emphasis on the reuse of wood in construction projects, and recycled wood as raw material in today's wood industry.
